If you are involved in manufacturing, you must understand workforce availability and the cost of labor. Work costs are the largest component in your overall cost of goods sold, and managing labor costs directly impacts your bottom line. Here is a quick guide to the cost of labor.
What Is Direct Labor?
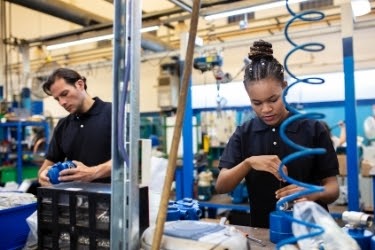
Direct labor costs are those associated with workers whose work directly impacts your factory's production of goods. These are the assembly line workers. The cost of labor includes hourly wages, employee benefits, and employee payroll taxes expended by the company on this portion of your workforce. Direct labor makes up a significant portion of your cost of goods sold, so you must identify essential labor appropriately.
What Is Indirect Labor?
Similarly, indirect labor costs are those labor costs associated with all the other employees in your company. Anyone not directly engaged in producing your product should be included in the indirect labor pool. This consists of those who perform maintenance on the company's equipment, human resource personnel, customer support, information technology, and sales. Indirect labor is part of your overhead, along with things such as rent, depreciation, and advertising.
Factors That Impact The Cost Of Labor
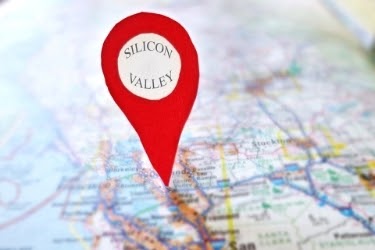
Just like real estate, the first concern is location. Your operation’s area has a considerable impact on the supply of labor and the cost of your workforce wages. Labor supply and demand vary regionally, so it is crucial to understand your local labor market.
The difficulty of the work also impacts the cost of labor. Unskilled workers are generally less expensive to hire and train for simple jobs. But experienced workers, such as those that required technical skills, are more costly to acquire and maintain.
The efficiency of your plan operations is another factor. Companies should do their best to identify and eliminate bottlenecks or poor manufacturing practices to increase efficiency. Labor costs can be cut dramatically by improving overall process completion times.
Employee engagement and morale are also meaningful—increased wages due to overtime, which has resulted from high absenteeism, hurt labor costs. A happy workforce is a more productive workforce, and that is good for your bottom line. Do not be afraid to throw the rotten apples out of the barrel.
Managing Key Issues That Impact The Cost Of Labor
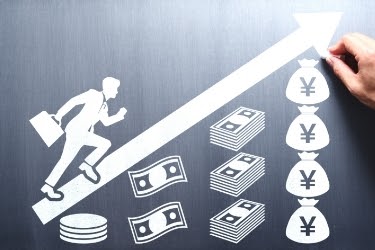
Wages increase over time for skilled workers. It is crucial to evaluate the costs of training new employees versus retaining current employees. If you are employing mostly unskilled labor, there are fewer incentives to try to keep workers. However, if your processes demand highly skilled employees, it is often much cheaper to increase wages and retain the current workforce than to bring new labor in off the streets.
Yet again, this will vary based on your labor supply of skilled and unskilled workers in your regional market. All of this must be carefully evaluated when making decisions on how to control labor costs.
Resources Available To Assist In Managing The Cost Of Labor
To help you understand your regional labor market, the United States Bureau of Labor Statistics has a plethora of information on their website. Their analysts have done exhaustive research on many of the factors discussed above. Because your labor needs and labor supply vary widely by industry, it is recommended that you consult the bureau's information to assist you with determining the actual cost of labor in your regional market.
Strategies For Managing Labor Costs
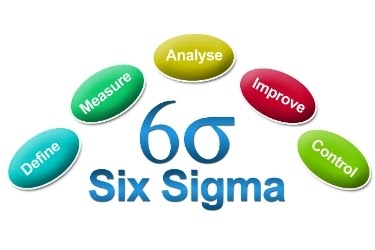
All manufacturing businesses can benefit from implementing a Lean Six Sigma program. Lean Six Sigma is a team-based methodology whose goal is to improve efficiency and reduce defects in an organization by optimizing its processes.
One example would be to examine warehouse layout optimization to reduce the amount of time it takes to move raw materials to the assembly line or finished goods to the loading dock. By improving the amount of time or the number of personnel required to perform these tasks, you can directly impact your labor cost.
Key Take-Aways When It Comes To The Cost Of Labor
- Direct versus indirect costs impact profitability in different ways.
- Labor markets are different based on the region of the country.
- Several indirect factors, such as employee morale, absenteeism, and turnover, can impact your labor costs.
- Whether your workforce is skilled or unskilled makes a bit of a difference.
- Process improvement initiatives such as Lean Six Sigma can help you root out waste, minimize downtime, and increase efficiency, thus improving your direct labor costs.
Hopefully, this guide has helped you understand workforce availability and the cost of labor for your organization. By reducing labor costs and managing the issues unique to your regional market, you will increase profitability long term. Call us today to learn how pallet pick up and delivery can improve your operational efficiency.