In today’s cutthroat business environment, the speed with which customers receive their orders often determines whether or not they will ever order from a business again. This especially applies to commonly found products with similar prices, where order delivery speed is the only thing that differentiates companies from each other in the customers’ minds.
The picking process is usually where the overall order fulfillment process experiences a bottleneck or a slow-down. Getting the picking process up to a competitive speed while minimizing human error is of utmost importance.
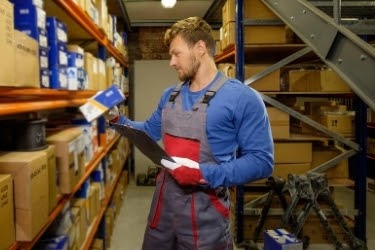
Factors such as warehouse organization, inventory management, automation, and computer software create an efficient warehouse that makes the picking process quick and accurate. We’ve consulted many supply chain experts and have a relatively comprehensive list of today’s best warehouse picking best practices.
Warehouse Organization
You need to do a few key things when organizing a warehouse to help streamline the picking process and maximize the real estate that you have.
You’ll want to:
- Store less needed items vertically, upstairs, and downstairs.
- Automate to maximize cube density.
- Plan for growth.
Layout Inventory In Picking Routes That Work Well With Your Picking Strategy
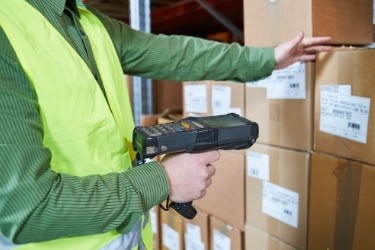
There are many picking strategies to choose from. Consider your picking strategy when deciding where to put the various inventory items, creating your pick “path.” Warehouse Management System (WMS) software would help you with this. You need to remember to slot particular inventory items according to demand, accessibility, safety, and ergonomics, though.
Use Bins, Containers, And Pallets For Kitting
Certain groups of items are commonly picked together. They can be palletized or otherwise kitted (pre-picked and grouped/stored together) by pickers working on off shifts.
Assign A, B, And C SKU Velocity Classifications
Classify SKUs so they can be correctly slotted. Classify with:
- The fast-moving ones (A) located close to the shipping area
- The moderately-moving ones (B) found a little further away from the shipping area
- The slow-moving ones situated the furthest away from the shipping area
Sophisticated WMS software can look at sales data and automatically classify and mark SKUs for you. It can also create move tasks and assign these tasks to people.
Create Multiple Zones
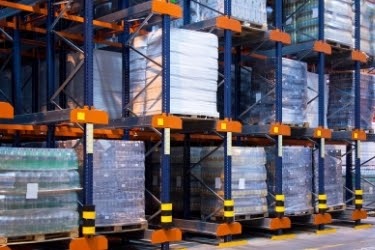
A grouping of pick locations makes up a small area called a zone. Create zones for picks containing items that can be confined to a small space to cut down on pick time. Ideally, you would also assign a picker to each zone, facilitating speedy picking by each zone’s picking specialist.
Assign non-conveyables (SKUs that cannot ride the conveyor) and the non-sortables (SKUs that cannot ride the sorters) to a zone. That way, they can be picked and shipped separately from the other items in the orders they are a part of. This prevents picking bottlenecks.
Install shelving and include other storage places that suit your processes and your facility
Provide bins, totes, kanbans, and pallets for kitting and other purposes. Plan space for those things too.
Use Signs To Stay Organized
Certain items can end up stashed wherever particular people would prefer them to be. There would be no question where everything goes if signs are installed.
Warehouse Inventory Management
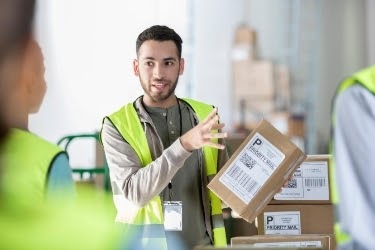
Traceability tips:
- Never mix SKUs
- Use inventory management software
- Use RFID technology to track shipping platforms such as pallets (contact pallet manufacturers)
- Use label printers
- Use unique tracking numbers
- Keep a good eye on expensive inventory
- Make sure the numbers are known after you track inventory
Replenishment tips:
- Keep inventory lean
- Use minimum order quantities to ensure there will never be short picks/stock-outs
- Plan for the timely replenishment of inventory
- Use off-shift personnel to replenish inventory
Cycle counting tips:
- Do daily cycle counts to ensure inventory accuracy
- Reassess how you do your cycle counting
- Use weigh scales for counting small bulk items
Inventory handling tips:
- Create an inventory handling process
- Create a way to prevent theft
- Document a returns handling process
Various other inventory tips:
- Calculate the cost of floor space
- When inventory levels shift (according to season or some other predictable reason), re-allocate storage space
- Use various storage strategies
- Regularly review SKU velocities (and move the affected SKUs to the appropriate locations)
Warehouse Picking
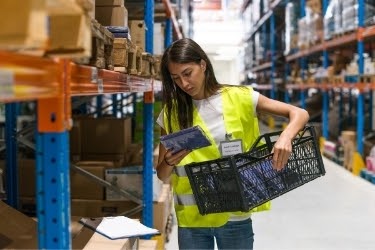
Picking tips:
- Touch picked items just once
- Pick directly into a shipping container, if possible
- Calculate the cost of labor
- Provide dynamic, proper equipment to warehouse workers
Picking strategy tips:
- Use the right picking strategy for your warehouse’s design and your needs
- Change your picking strategies as the business grows
- Use a third-party pick and pack fulfillment service if necessary
- Create picking routes that suit the picking strategy being used.
Picking strategies:
- Pick and pass
- Wave
- Task-based
- Parallel
- Split case
- Batch/cluster
- Sequence
- Color
- Voice
- Zone
Ways to motivate pickers to pick faster:
- Use engineering labor standards.
- Use gamification techniques
- Use good ergonomics
Automated picking technology types:
- Goods-to-person technology (improves ergonomics)
- ASRS and other picking machines (reduces costs and picking errors, is safe and efficient)
Computer-assisted picking technology options:
- Hands-free order selection
- Bar code scanning
- Scan verification
- Parts picture database
- Light-directed technology
- Pick-to-light technology
- Put-to-light indicators
- Electronic picking tickets
Data tips:
- Establish key performance indicators
- Conduct an “ABC” analysis
- Use measurement best practices.
- Use automatic data collection.
- Use statistics to increase productivity.
- Identify the “slow kid.”
- Use data to make decisions.
Other picking tips:
- Avoid paper-based picking processes.
- Increase operational visibility
- Create a reliable documentation system
- Create a learning culture
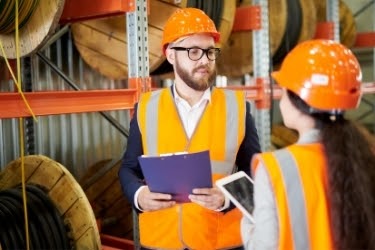
Warehouse Safety
Safety tips:
- Keep aisles clear and workspaces clean
- Use ergonomics
- Understand hazards
- Provide training certifications
- Automate wherever possible
Warehouse Maintenance
Maintenance tips:
- Keep spare parts on hand
- Plan preventative maintenance
- Audit often
- Review SKU velocity often
Warehouse Shipping And Receiving
Shipping and receiving recommendations:
- Receive directly into open orders
- Establish and review the receiving process
- Establish a returns management process
Warehouse Software
Software tips:
- Use the appropriate warehouse management system (WMS) for your needs
- Sync your WMS with your enterprise system (ERP)
Pallet Market, Inc is the leading pallet manufacturer and distributor in Southern California. Let us help you with your warehouse picking best practices pallet needs. Contact Pallet Market, Inc. for a pallet online quote.