If you work in warehousing and logistics, you already know how crucial warehouse space optimization can be for efficiency. You also know that optimizing warehouse floor space can make or break operations when unforeseen challenges arise. Having a plan in place before things get hectic is important, meaning now is a good time to begin planning a warehouse layout that can scale, adjust, and flex with changing needs.
Of course, making these changes is often easier said than done. The fact is that there’s a lot that goes into planning warehouse storage space, and there’s often even more that goes into redesigning existing warehouse storage space. If you feel like you’ve hit a wall when trying to improve warehouse space optimization, consider the following tips and strategies for more efficient warehouse operations:
Evaluate Your Pallets and Racks
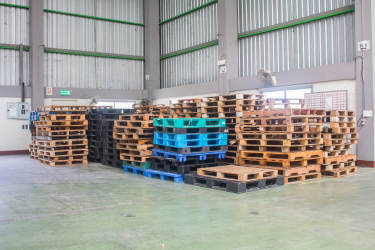
Pallets, racks, and other storage solutions are used across virtually every warehouse in the country, but the efficient use of pallets and racks is one of the keys to increasing storage capacity. Your goal should not be to merely use your available space. Instead, your goal should be to find ways to maximize the use of your available space. One way to maximize warehouse space utilization for pallets and racks is to use vertical space.
This is where the types of pallets and racks used in your warehouse come into play. You need to find solutions that can be safely stacked and utilize your space efficiently. This doesn’t necessarily mean stacking pallets on top of one another, as this may not be ideal depending on the items on each pallet. Instead, look for pallet racks that offer additional support mechanisms to accommodate stacking to free up space.
Saving Money While Saving Space
Taking steps to maximize available space by evaluating your pallets and racks can potentially free up space, and as an added bonus, you may be able to reduce operational costs by making changes to the types of pallets and racks your warehouse uses. Evaluate your current supply of pallets and racks. During this evaluation, you may find more cost-effective alternatives. A new supplier of pallets may be able to introduce you to products that can provide the same level of service at a lower cost.
Utilize Pallets Wisely
Additionally, take a look at the inventory you have coming in to see if you are utilizing rack space efficiently. If you end up with half-full pallets stored in locations where completely full pallets should be, you lose half of your storage space in these areas. If possible, consider changing the palleting of certain items to utilize space efficiently instead of placing half-empty pallets in storage areas. Remember that other solutions exist that will better use your storage spaces.
Look for Opportunities to Reduce Wasted Space
Wasted space is a big productivity and efficiency killer in warehousing and logistics. When you fail to use your available space efficiently, getting pallets processed and orders routed to their destinations typically takes longer. Losing pallets and orders is also easier when warehouse space is not used efficiently.
A Practical Example: Narrow Your Aisles
For example, take a look at aisles to see if there are opportunities to make them more narrow without compromising safety. Narrow aisles may be able to make more efficient use of your floor space, but this must be done in compliance with safety regulations. You also don’t want to make aisles so narrow that you jeopardize the integrity of pallets and inventory. If aisles are too narrow, you run the risk of accidents and injuries and difficulty maneuvering inventory.
Evaluate Inventory Throughout the Process
Wasted space may also be found in the form of inefficient processing. If you route incoming pallets across your warehouse for storage instead of storing them closer to your intake areas, you may not be utilizing space in the most efficient manner. This equates to wasted space, as the space closer to your bay doors could be a more efficient option.
Instead, consider a first-in-first-out (FIFO) approach. This may require rearranging your current storage space and processes, but it will ultimately save storage space and increase efficiency. When looking for wasted space, try to think about the processes of your warehouse from start to finish. You’ll also want to consider how each interaction or touchpoint affects every other step in inventory handling.
Employ a Warehouse Management System
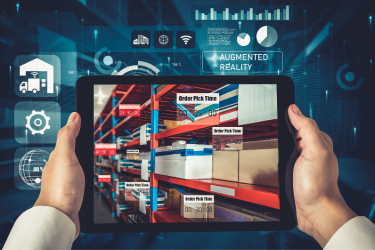
Technology can be a huge asset in warehouse storage space optimization. A warehouse management system that utilizes artificial intelligence (AI) to analyze available storage may be able to find space-saving opportunities that you and your team have overlooked.
These systems can also analyze historical trends to provide options for space optimization and storage systems that change based on seasonal shifts, staff rotation, and increased throughput due to other circumstances. As time goes by, these systems can provide updated recommendations for space optimization based on your changing needs.
Communicating Across a Supply Chain
Warehouse management systems are also beneficial in sending alerts to warehouse managers and communicating with other links in your supply chain. If a logistics partner uses the same management software or software written by the same developer, you may be able to integrate your warehouse operations more deeply into your supply chain through communication with these supply chain partners.
If changes are made to storage or processing, your software communicates these updates further down the supply chain, where adjustments can be made. This can change the pace at which pallets arrive at or leave your warehouse, allowing you to make more efficient use of storage space.
Update Employee Training
Your floor workers, dock workers, and every other employee with contact with pallets and inventory are your eyes and ears on the floor. These professionals work with inventory daily and usually make on-the-spot decisions about how to handle pallet routing and inventory storage.
While you may have an employee manual that documents your standard operating procedures, now would be a good time to think about reviewing this manual. If you haven’t updated your policies and procedures in several years, you may not realize that some outdated policies are causing inefficiencies in inventory storage.
Ask Workers for Input and Feedback

When revisiting your employee manual, try interviewing key workers for their opinions. Because these frontline workers have hands-on experience processing pallets, they may be able to provide important insight into policies that could be improved upon.
If you receive critical feedback from workers about your storage procedures, recognize this feedback as a valuable tool. An employee who cares enough to notice that things could be improved is an employee who cares about their job and the company.
Look for Solutions to Temporarily Store Overflow
As mentioned above, the flow of traffic in and out of a warehouse can change throughout the year, and as evidenced by the Evergiven Suez Canal obstruction of 2021 or the COVID-19 pandemic, certain events can cause massive, rapid changes in logistics and routing. Instead of forcing overflow inventory into existing warehouse space, consider utilizing temporary storage space in the form of trailers or cargo containers.
These modular and portable solutions can provide extra space as needed, and they can be stored at your warehouse site or relocated as needed. When overflow becomes a problem, use these solutions to handle excess inventory, always loading pallets that aren’t planned to ship anytime soon first. You can then relocate these trailers or containers to a nearby or regional site with plans to retrieve them when it’s time to process the inventory stored inside.
Avoid Using Overflow Storage as Regular Storage
As a precaution, avoid using overflow storage as normal storage. It can be tempting to start placing regular inventory in overflow storage areas as a matter of process, but if a true overflow situation pops up, you will be in for some trouble.
Instead, try to forget that the additional space exists unless and until it is needed. Much like putting money away into a savings account straight from a paycheck, you won’t miss these extra resources if they aren’t placed in regular rotation.
Partner With a Consultant
Lastly, if you implement a combination of the suggestions above and find that you still have difficulties with optimal warehouse storage, it may be time to bring in a consulting partner specializing in warehouse space, storage, and logistics. Consultants in this arena typically have experience in warehouse management, warehouse management systems and software and supply chain and logistics management.
One benefit of working with a consultant to maximize your warehouse space and improve efficiency is receiving a customized plan. Although the suggestions offered above provide a broad view of the subject of warehouse space management, not all apply to every warehouse. Your situation is unique, and receiving personalized guidance from an experienced expert can typically create a more effective outcome than following general advice alone.
Contact Pallet Market Inc to Learn How Our Pallet Experts Help Warehouse Professionals Get More Done
Pallet Market Inc provides a range of resources to professionals in the warehousing and logistics industries, including pallet pickup and repair. Whether you need to buy new pallets, discuss changes to your existing pallet needs, or find additional solutions to warehouse space optimization, Pallet Marketing Inc is the partner you can count on.