Inventory control is achieved in a warehouse with strategic preparation. Your warehouse design should take into account space optimization and which products are most likely to move the fastest. You may have to adjust your strategies depending on the season. Follow these warehouse management tips to improve your overall operational efficiency.
1. Start with Warehouse Organization
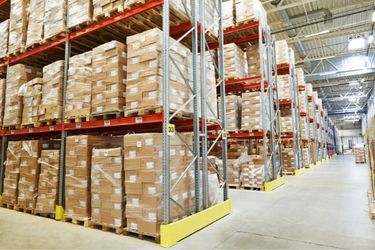
One of the most important warehouse management tips is to organize your supplies in a way that's easy for moving products in and out. Paying attention to accurate inventory levels is another basic key to proper warehouse organization. Accuracy and cleanliness should be maintained at each shipping station.
Your warehouse inventory should be arranged in a way that makes it easy to move high-demand items in and out quickly. Structuring the warehouse so that packing and shipping areas are near each other helps accelerate shipping. Aisles should be free of clutter and safe for transporting items.
An important part of the organization is quality control to make sure what leaves the warehouse is based on accurate order picking and packing. Here are other important items that should be on your checklist for maintaining an organized warehouse.
Maintain a Clean Environment
It's important to file away documents in proper places at the end of each day so that they don't stack up and contribute to clutter. It only takes a few hours per week to ensure a warehouse is generally tidy. Keeping your warehouse clutter-free reduces the chances of lost orders and accidents that can lead to employee injuries.
Use Lean Inventory Strategies
By only housing relevant inventory, you can keep your warehouse from becoming cluttered with items that don't help the bottom line. Limit orders to what you need based on demand rather than accommodating a vast universe of untested products. Order only the amounts you need, which allows for storage flexibility. By adopting lean practices, you'll be preparing for sustainability, which will help cut storage costs.
Establish a Consistent Labeling System
Label your inventory in a consistent way that makes it easy for workers to find and identify products. Warehouses commonly label inventory with SKU (stock-keeping unit) numbers along with product names and descriptions. The easiest way to take the guesswork out of locating products quickly is with a handheld barcode scanner. You need to keep detailed records of your inventory items, which is best achieved using a warehouse management system (WMS) software platform.
Pay Attention to Delivery Deadlines
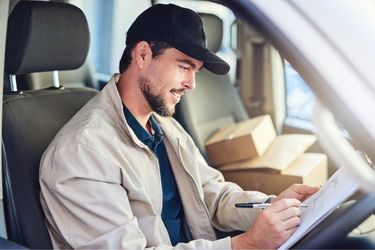
Don't let old orders stack up, which can lead to late deliveries. If your company experiences a labor shortage or lacks the capacity to ship orders at a rapid pace, consider outsourcing to a third-party logistics (3PL) firm. Modern 3PLs invest in automation technology that helps speed up logistics processes.
Paying attention to delivery deadlines will affect how you prioritize items, which often involves the ABC Analysis method, in which "A" items are prioritized due to the highest monetary value.
2. Warehouse Layout Essentials
An effective way to save time and warehouse space is to consider layout, shelving, and space utilization so that you maximize storage space. Stackable shelf bins contribute to maximizing space allocation. Use container and pallet sizes that allow you to store units securely and safely. Your team will spend less time and money on labor if the warehouse layout allows for easy mobility.
There is no one-size-fits-all layout that works for any warehouse. Each warehouse has storage capacity in which space must be allocated as efficiently as possible. Some warehouses have plenty of shelving while others rely on carefully positioned pallets. The main point to remember is that inventory must be easily accessed, which means avoiding obstructions.
Another key to an ideal warehouse layout is for there to be plenty of open space devoted to areas set up for receiving, packing, storage, and shipping. There should also be ample space for administrative offices. Remember that square footage is expensive, so it's important to maximize as much vertical space as possible.
3. Choose Streamlining Technology
It's crucial to invest in a WMS to stay competitive in the logistics industry. A WMS is a key to accurate and easy-to-locate inventory. You'll be able to track every item through a scanner that communicates with RFID chips embedded in each product. You can streamline your warehouse much more easily with a WMS that integrates with smart technology that generates real-time data.
Today's warehouses must be set up as agile operations so that orders can be processed quickly. The ability to find a specific item instantly with a WMS and scanning tools allows a warehouse to compete for customer satisfaction. Warehouses lacking a WMS, however, are destined to fall behind the competition.
Automation and AI are becoming norms in many high-end factories. Research from Boston Consulting Group projects that 1.2 million robots will work in manufacturing plants by 2025. There will still be a need, however, for analysts to evaluate the performance of robots. The use of IoT devices is expected to expand enormously, giving producers real-time data that can help speed up decisions on production adjustments.
The more a warehouse can measure the results of its processes, the better chances it has of overcoming systemic vulnerabilities. Warehouse decision-makers should choose technology carefully to focus on improving operational efficiency rather than invest in trends that don't help the bottom line. They should be aware of the various technology options available including voice-activated solutions.
4. Pick and Pack Speed
The amount of time your team spends on the pick and pack process has a huge impact on costs. Organizing pick lists is one of the keys to achieving time efficiency. It's helpful to optimize the pick path and prioritize order picking to improve picking productivity. Picking and packing efficiency in warehouse environments comes down to establishing pick locations that reduce travel time and provide easy access to picking bins.
The order picking process can be accelerated with WMS software. It will allow you to sequence orders according to the pick path or sections of your warehouse. You may need different types of picking methods depending on the type of order, such as single order or multi-order. The more you arrange inventory in a manner that reduces the amount of walking a picker must do, the more you help streamline and speed up the picking process. It helps to arrange inventory based on picking frequency.
Another dimension to picking and packing that must be considered is communication. Personnel handling inventory should have all the necessary product information available to them to complete orders accurately.
5. Improve Efficiency and Productivity
One of the most important goals of warehouse management is to reduce operating expenses while increasing warehouse productivity. Running a warehouse efficiently is important because of the amount of space it occupies and the energy it consumes.
You can cut labor costs by using automation technology that replaces boring, tedious, or dangerous tasks. This investment alone will improve warehouse efficiency by reducing downtime and allowing workers to spend more time on activities that technology cannot perform better. With the right software platform, you'll also reduce employee errors that slow down the order fulfillment process.
Another idea for maximizing warehouse inventory efficiency is cross-docking, in which products are shipped directly from the manufacturer or supplier to retailers or customers without much storage time. It typically involves receiving products at a dock and then moving them to the outbound side of the dock to ship out.
6. Maintain a Safe Warehouse Environment
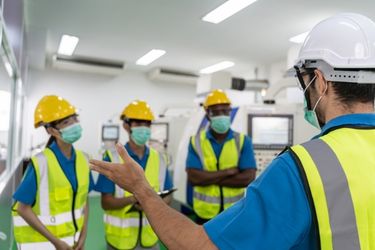
Another key to maintaining a successful and productive warehouse is to make safety a top priority. The safer your work environment, the fewer sick days your staff will encounter and the fewer workers comp insurance claims your company will file. Part of fostering a safe work environment is creating a friendly team atmosphere in which each member respects the well-being of other coworkers.
Regularly training staff members about how to handle new products helps reduce confusion and bottlenecks. Keep in mind that no matter how innovative your technology is, people are what make inventory move from one location to another. So it's best to promote an upbeat work experience that goes with a healthy work-life balance to reduce the odds of worker burnout.
Making the warehouse a comfortable workplace environment will help inspire workers to do a good job. That means the facility needs proper airflow to avoid breathing problems. It helps if some of the facility has soft flooring to give workers a break from standing on hard flooring. Providing workers with incentives will help motivate them to focus their energy on the job. It's also imperative to keep dangerous chemicals under control so they don't cause illness among multiple staff members.
Conclusion
The key to efficient supply chain management begins with logistics firms committing to the organization, technology, and hiring the right people. Your warehouse will run much more smoothly if you invest in training people to run your technology efficiently. Learn more about warehouse management tips and how part of improving logistics is using the best pallets.