To determine the cost of inefficient picking and its impacts upon your business, it is necessary to understand the picking process. What factors influence the cost of selection? What are the benefits of picking efficiently? How can you increase your picking efficiency? Continue reading to find out the answers to these questions and more.
What Is Picking?
Picking is one aspect of the order fulfillment process within your warehouse. Order fulfillment is one of many warehouse processes that can be managed through a Warehouse Management System (WMS). Picking has a direct impact not only on order fulfillment but also on inventory management and customer satisfaction.
How To Determine The True Cost Of Inefficient Picking
Once you know the cost of picking an order, you can determine how higher pick rates will add to your bottom line. You can choose the approximate cost of selecting an order by calculating the labor cost divided by your pick rate. For example, if an order picker makes $20 per hour, and your pick rate is 40 orders per hour, the cost to pick an individual order would be $0.50 per order. If your picking efficiency (pick rate) increased to 80, your cost per order picked would be cut in half.
The Benefits Of Efficient Picking
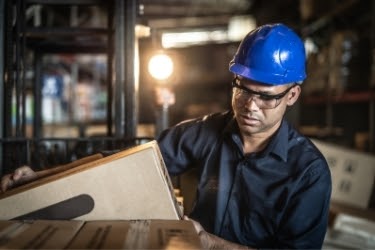
The above example is one of the tangible indicators of increased picking efficiency, but there are intangible impacts. The primary one is increased customer satisfaction, which is driven by more efficient picking, fewer mistakes in orders, faster shipping times, and better overall inventory control.
Higher pick rates also result in lower labor costs and reduced maintenance expense for the picking process machinery. By improving route efficiency, pickers spend less time per order, and machines travel fewer miles within the warehouse when picking orders.
Factors That Influence The Cost Of Picking
• Warehouse size
• Complexity of the order to be picked
• Cost of labor
• Route efficiency
• Pick rate (# of orders picked per hour)
Common Picking Problems
The following is a list of common picking inefficiencies. When addressed, these can radically improve your picking processes.
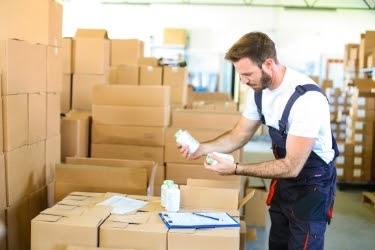
Human Error
Manual picking can result in incorrect pieces being picked or inaccurate quantities of items being selected. This can result from improper inventory storage, or it could be due to the lack of a warehouse map or delineated locations for goods waiting to be picked.
Picked Items Cannot Be Located
Whether items were stowed incorrectly or mislabeled, an item must be able to be located to be picked efficiently. This also leads to human error if the picker does not validate the item being picked but merely grabs the location.
Inefficient Picking Routes
Processes that rely on the selector’s best guess regarding navigating the warehouse result in multiple routes for picking an order. This means that the selector drives aimlessly from one location to another, gathering items for an order without any attention to the shortest route through the warehouse. This wastes both labor and machine time.
Manual Or Paper-Based Picking Processes
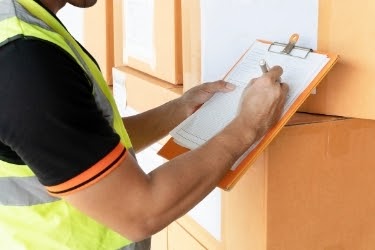
Manual or paper-based picking processes are inefficient because most do provide an audit trail of who picked the order, when it was gathered, or the order in which it was selected. Paper or manual processes are also fraught with inventory management errors, as it is easy to overlook or record incorrect quantities of items picked.
No Contingency For Partially Picked Orders
If an order cannot be picked in its entirety for any reason, there must be a contingency for partially-picked orders. Without contingency for selected orders, orders can be lost, shipped prematurely, or picked more than once, rather than picking up the first attempt left off.
Your Processes Rely On Worker Experience/Memory
Smaller warehouses may rely on picker experience when fulfilling orders. As your business grows, this becomes an obstacle to efficiency because workers may not remember where everything is located. Without a warehouse map, temporary or contract workers do not know where to pick orders and spend inordinate amounts of time just trying to find pieces for the order.
Overall Lack Of Automation
Automation, by its very nature, is more efficient than any manual process. By leveraging the latest technology and equipment, you can quickly increase your pick rates by up to a factor of 5x. A 500 percent increase in pick rate will have a significant positive impact on your bottom line.
How Can You Increase Picking Efficiency?
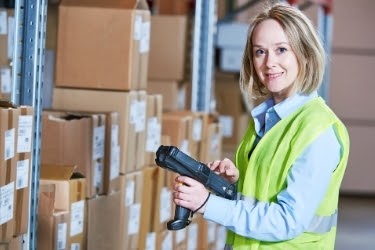
Short of bringing in a Lean Six Sigma expert to evaluate your warehouse operations, here are a few things you can do to improve your picking efficiency.
Document all of your warehouse processes. Nothing should be in someone's "head." Everything needs to be recorded somewhere so that if anything happens to key employees, your warehouse does not become a shambles.
Make your process documentation readily accessible to all relevant employees. It doesn't do any good to have the processes documented in a notebook stored away in a file cabinet somewhere. It needs to be in the hands of your selectors. This allows them to operate more independently and solve their minor issues when problems arise.
Develop contingency plans for the most common problems that occur in your operation. Document these and distribute them with all the other process documentation. This keeps everyone on the same page and ensures that outliers will be resolved consistently.
Automate as many of your processes as possible. There are many great Warehouse Management Systems on the market today that can help you with everything from warehouse mapping to inventory control.
Install automated pickers/conveyor belt systems to reduce the cost of manual picking. You can also investigate voice-controlled selection and mobile apps designed to help with picking and inventory management.
Engage your workforce. Often your best employees have insights from the day-to-day job that management night not ever see. Some of the best suggestions may come from the veteran of 20 years and the new employee looking at things from a fresh perspective.
If you are wondering where you can get pallets, some companies focus on supplying pallets to businesses. Recycled pallets can also be an option, but those are much harder to come by.