A well-organized retail business emphasizes inventory management techniques and best practices to achieve a highly efficient operation. Inventory management is a crucial link in the supply chain, as it involves sharing data with other suppliers. Here's why each link in the supply chain needs to maintain effective inventory management.
How Important Is Inventory Management?
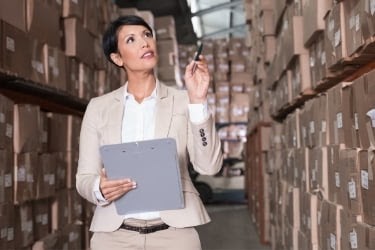
Studies have shown that nearly half of retailers make inventory management their top priority daily. It involves tracking quantities to ensure you can meet market demand. Many companies are moving away from manual tracking methods in favor of more accurate digital tracking methods based on the placement of IoT sensors. These days shipped products typically contain RFID chips that communicate with logistics systems to track where an item is located at any given moment of the journey.
Manufacturers embracing digital transformation use inventory management software to organize warehouses and distribution centers. Last century it was much easier for a shipped item to get lost somewhere in the supply chain until barcodes helped track each unit. Even then, the item might still come up missing due to theft within the supply chain. Now thanks to IoT sensors, it's possible to know precisely where and when a unit came up missing.
When inventory is well managed, the rest of the supply chain operates smoothly. But when it's disorganized, all kinds of errors can occur, such as shipping products to the wrong location or ending up with overstocked low-demand supplies or out-of-stock high-demand supplies. Furthermore, warehouse shelves need to be labeled correctly while inventory items are appropriately placed.
Greater Storage Efficiency
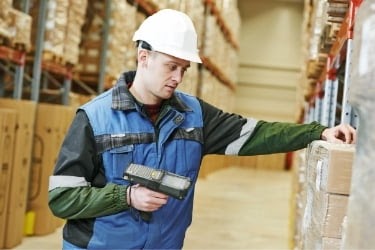
A significant reason for a retailer or wholesaler to invest in an inventory management platform is to achieve better storage efficiency. Some manufacturers have multiple warehouses in a market and operate most efficiently when each warehouse shares inventory data. Knowing where to locate specific products helps make the shipping process more agile and seamless.
It's crucial to bring redundant warehouse processes under control, which can be achieved with an inventory management platform. Redundant processes that create wasteful production costs can be eliminated when you deploy a database that tracks inventory, storage locations, and employee schedules in a centralized place.
Labeling and barcoding help reduce inventory redundancy. Developing an efficient warehouse layout is further helpful in cutting down on unnecessary redundancy. Using a well-planned warehouse configuration is key to optimizing labor and scheduling equipment use.
ABC inventory analysis will help place items in storage based on their demand to find the most popular items most quickly. This design also accommodates restocking efficiency. Meanwhile, seasonal or less popular items can be placed out of the way so that they don't slow down the transport of more active products.
Developing standard procedures expressed in a training manual is the most effective way to run a warehouse. The standard procedures should eliminate redundancies and other inefficiencies. Part of these procedures should involve steps for troubleshooting when bottlenecks occur.
Inventory Management Techniques
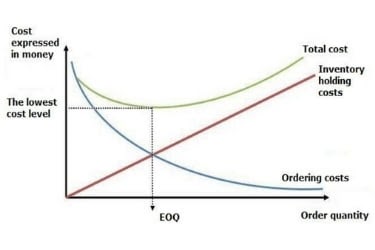
Economic Order Quantity - Warehouses can implement a variety of inventory management techniques that enhance the supply chain. Economic order quantity (EOQ) is a formula that generates the ideal number of units a company should order for each product. The variables for determining the right amounts to order include production costs and demand. EOQ is used to reduce bulk costs, as it seeks to determine the maximum units to purchase that will create the most space availability and overall efficiency.
Minimum Order Quantity - MOQ is the inverse of EOQ as it seeks the lowest amount of unit volume for inventory due to its limited demand. It's common for products that cost more to manufacture to have a smaller MOQ than lower-cost items. This equation might be applied to niche items with minimal demand.
Dropshipping - This popular third-party shipping method is used by online businesses that mostly showcase merchandise digitally and handle online transactions for orders fulfilled by another entity such as the manufacturer. Dropshipping is an attractive fulfillment method due to its low risk for entrepreneurs who mainly need to maintain a low-cost website that generates leads.
Consignment Inventory - Instead of purchasing inventory upfront, a wholesaler or vendor deals with retailers that allow stores to showcase or hold goods at no cost. Its consigner still owns the inventory until a purchase is made. This method helps test new products.
Just-In-Time (JIT) Inventory - JIT is an effective strategy for arranging raw material orders according to production schedules. This method not only cuts inventory costs but also provides supplies on an as-needed basis. It avoids allowing deadstock to build up, which takes up costly space.
Safety Stock Inventory - This method provides a surplus of products when needed to meet demand. It's used during a shortage or when an item is expected to sell well. Wholesalers may use this method to offset incorrect forecasting or unexpected shifts in demand.
FIFO and LIFO - Both "first-in, first-out" and "last-in, last-out" are valuable methods for figuring out inventory costs. FIFO is based on selling older inventory first, while LIFO emphasizes the selling of newer stock first. Deciding between these options might come down to the durability of the product.
Perpetual Inventory Management - This basic inventory method involves counting shipped units as they come in. It's the most commonly-used inventory method because it can be done digitally or with pen and paper.
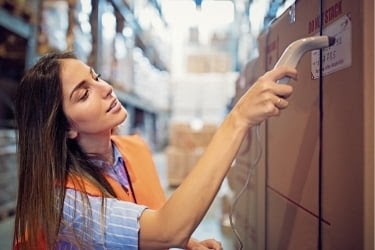
Batch Tracking - Putting various similar items in a group called a batch is commonly used for quality control purposes in inventory. It's ideal for monitoring when inventory items expire or identifying defects within the same batch.
Lean Manufacturing - The concept of lean production is spreading across all industries as a path to sustainability or minimalism. Lean management practices lead to more efficient production and waste reduction. This method might involve cutting certain supplies that have low demand or cause public controversy.
Six Sigma - This tracking concept and tools focus on standardization and business flow to improve revenue while decreasing excess inventory. Motorola developed the process in the eighties, then General Electric in the nineties. It helps nurture management talent and provide hands-on management experience while tracking DMAIC (define, measure, analyze, improve and control) data.
Cross-docking - In this scenario, no or minimal inventory is stored as items are moved from one truck to another. Incoming truckloads are merely transferred to another vehicle, which is evident when items from a large retail truck are moved to another vehicle at one of the brand's distribution centers.
Bulk Shipping - This inventory technique relates to cutting costs when massive metric tonnes of cargo are shipped. It might involve sending several items in a large bulk container that stores unpackaged solid or liquid goods. The shipment in this scenario is usually measured according to volume as the three main steps are unloading, storage and loading.
Demand Forecasting - Retailers often use this common management technique for estimating product popularity. It's based on analyzing historical customer sales data or other information on trends to ensure enough stock is available to meet short-term demand.
Keys To Successful Inventory Management
The most effective way to conduct inventory management is to set visibility and organization goals that facilitate more automated or streamlined customer pick-up. It requires investing in intelligent technology and carefully managing inventory software. Sorting out active from deadstock is one of the critical benefits of maximizing warehouse space. Using before and after performance data to make comparisons is a significant step toward determining the best techniques to help streamline your operation.
Successful inventory management can be measured by various counts such as mis-shipments and mis-picks. The more you see dead stock disappear, the closer you are to achieving inventory efficiency. Ultimately, the better organized your warehouses are, the faster you'll be able to serve customers, which is then reflected in online reviews.
Conclusion
The above inventory management techniques and strategies can help you organize your warehouse or distribution center effectively. Setting up the proper layout and system for your needs will help move your company toward achieving inventory sustainability. And, if you’re looking for quality pallets in California, contact the experts at Pallet Market, Inc.