Paste The global marketplace dynamics have been shifting beneath our feet, evolving at breakneck speed to accommodate e-commerce eruptions and the modern consumer’s insatiable appetite for immediacy. In this maelstrom, warehouses stand at the heart of the supply chain, acting as the conjurers of swift fulfillment, impeccable stock management, and cost-effective operations. Here, in this labyrinth of logistics, the true power of warehouse automation techniques shines through, changing the game from reactive to proactive, from labor-intensive to streamlined, and from error-prone to precision-led.
But it's more than just moving boxes. Automation in warehousing has become the linchpin of operational excellence, redefining how we manage inventory, pick and pack orders, and ensure the seamless flow of goods. In this comprehensive piece, we dissect the nuances of innovative automation technologies, offering logistics managers and supply chain professionals a treasure trove of insights to build the warehouses of tomorrow—today.
But before we unpack the tools of this trade, it’s pivotal to understand the driving forces behind the burgeoning need for advanced warehouse automation.
The Blueprint of Modern Warehousing
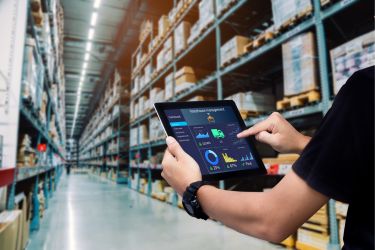
In the past, the warehouse was seen as a cost center – an operational necessity to store goods until needed. However, with the rise of e-commerce giants like Amazon setting the bar for next-day delivery, warehouses have transitioned from the periphery of business strategy to the crux of competitive edge. Speed, precision, and operational efficiency are the tenets of modern warehousing, and automation is the conduit that makes these tenets achievable.
The growing complexity of supply chain management accelerates the quest for enhanced efficiency. Modern warehouses juggle an intricate dance of globalized sourcing, fluctuating demand, and an expanded array of SKUs. Enter automation – the promise of reducing human error, enhancing precision, and boosting throughput, elevating the warehouse from perfunctory storage to a value-adding distribution center.
In a world that demands rapid responsiveness and error-free execution, warehouses have transformed into hives of technological innovation. Gone are the days when automation was synonymous with conveyor belts and forklifts. Today, warehouses hum with the orchestration of autonomous mobile robots (AMRs), sophisticated warehouse management software (WMS), and cutting-edge technologies like RFID and IoT, all designed to harmonize complex processes and drive profitability.
Unboxing Warehouse Automation Techniques
Autonomous Mobile Robots (AMRs): The New Workforce
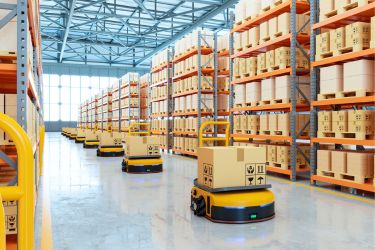
Traditional warehouses relied heavily on human labor, with its associated costs, limitations, and potential for error. Today, the Autonomous Mobile Robot is a new player in the workforce. AMRs herald a new era of flexibility and efficiency, as they are not tethered to fixed paths like their conveyor belt predecessors. These nimble robots chart their course through the warehouse. They can handle various tasks, from picking to packing to transportation and cleaning, leading to optimized pick paths and reduced order fulfillment times.
Enhanced Safety with Collaborative Robots (Cobots)
Safety is not a dispensable consideration but an imperative in pursuing productivity. Collaborative robots, or Cobots, are designed to work alongside human operators, augmenting their capabilities while adhering to strict safety protocols. By automating repetitive or strenuous tasks, Cobots reduce physical strain on workers while ensuring safety is not compromised. This new breed of robotic coworkers is not here to replace but to empower, providing a synergy that’s both productive and protective.
Real-time Inventory Counts with RFID and IoT
Maintaining accurate inventory counts in real time is a superpower in the warehouse ecosystem. RFID and IoT technologies empower warehouses with this capability. RFID tags on inventory and IoT sensors within the storage facilities automatically update the inventory levels, leading to a continuous and instantaneous reflection of stock, thereby reducing stockouts, overstocking, and the manual effort traditionally associated with inventory reconciliation.
Put-to-Light Systems Revolutionizing Order Fulfillment
Order fulfillment is a pivotal operation in warehousing, and put-to-light systems streamline this process with meticulous precision. When an order is received, products are retrieved and placed in a designated location with a light indicator, directing the pick-and-place action for efficiently sorting items and reducing picking errors. This accelerates the process and simplifies and reduces the cognitive load on warehouse staff, leading to a more enjoyable and efficient work environment.
Automated Sortation Systems: A Symphony of Speed
Warehouses with high volumes of similar products often grapple with the challenge of efficiently sorting and directing products. Automated Sortation Systems, encompassing a variety of methods such as conveyors, tilt trays, and pushers, harmonize this herculean task. Products are efficiently sorted based on predefined criteria like destination and delivery status. They minimize manual handling, decrease processing times, and eliminate the scope for human error in sorting, ensuring that orders reach their destinations promptly and accurately.
Automated Storage and Retrieval Systems (AS/RS): A Vault of Efficiency
AS/RS systems serve as beacons of space and time optimization for warehouses grappling with space constraints. These systems utilize computer-controlled systems to manage and retrieve goods from their designated storage locations. By eliminating the need for human intervention, AS/RS ensures precise and swift retrieval, optimizing space and time – two commodities warehouses can never have too much of.
The Brain Behind the Brawn – Warehouse Management Software
Warehouse management software acts as the maestro to orchestrate the symphony of automation. These systems control and manage the entire warehouse operation, from inventory management to order fulfillment, labor scheduling, and beyond. In addition to coordination, WMS provides crucial insights into warehouse performance, thereby enabling dynamic decision-making that’s indispensable in the cutthroat landscape of modern business.
Mastering the Art of Automation
Integrating Automation into Your Warehouse
Integrating automation into your warehouse operations is not uniform; it is tailored to each facility's unique characteristics and requirements. Starting with an in-depth evaluation of current processes to pinpoint inefficiencies, the step toward automation involves setting precise goals, picking suitable technological partners, and selecting the right equipment. This integration process should be gradual and iterative, evolving continuously with the warehouse's and business's changing demands. Training, engagement, and getting the buy-in of employees are crucial aspects. Automation enhances human expertise rather than replacing it. A pivotal factor in this transition is considering the standard pallet size for optimal storage and retrieval efficiency, ensuring your automation solutions accommodate the most widely used dimensions in the industry.
Adapting to the Tectonic Shifts in Warehousing
The warehouse of the future isn't merely a storage space; it is an intelligent, self-optimizing, and dynamic organism fueled by data, powered by automation, and directed by human ingenuity. The transformation is more than a technical upgrade; it’s a shift in mindset and operational ethos. It requires a commitment to continuous learning and adaptation, an entrepreneurial spirit to experiment with emerging technologies, and an unwavering emphasis on customer satisfaction.
The Proof Is in the Picking – Benefits of Warehouse Automation
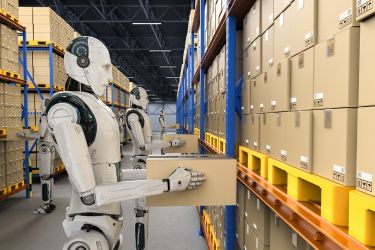
The value proposition of warehouse automation is tangible and multifaceted. It brings to the fore- a significant reduction in operational costs, an exponential increase in productivity, a drastic minimization of errors, a leap in efficiency, and a fortress of competitive advantages. It redefines the warehouse as a cost center and a strategic asset that propels growth and customer loyalty.
Navigating Uncharted Automation Territory
The avant-garde of warehouse automation is continually being pushed beyond current horizons. With the convergence of technologies like AI, machine learning, and advanced robotics, the possibilities are as limitless as they are exciting. For logistics professionals and warehouse operators, the challenge lies in staying informed, adaptable, and prepared to harness the full potential of these advancements.
The Symphony of the Automated Warehouse
The tale of warehouse automation is one of transformation, innovation, and relentless progress. It stands as a testament to the indomitable human spirit that thrives on the quest for efficiency and excellence. The future of warehousing is automated, but the heart that drives this automation remains resolutely human – aspiring for the perfect union of technological prowess and human endeavor.
The foray into warehouse automation techniques is an odyssey that shapes the very contours of supply chain management. To all those navigating this path, may your warehouses be as efficient as they are automated, and your journeys through this brave new world be filled with discoveries and fulfillment.
For more information on improving warehouse management and supply chain operations, stay tuned for our next post on ‘Streamlining Supply Chain Operations.’
If you are looking for a reliable pallet manufacturer, Pallet Market is one of the top pallet suppliers in Southern California.