The modern warehouse is more complex than ever, and following disruptions caused by the Covid-19 pandemic, warehouse managers are hard-pressed to find ways to operate more effectively. Lean warehousing is a concept that has become more popular as a result, and adopting lean warehousing means finding ways to make each element of your warehouse operations as efficient as possible without sacrificing quality.
How Do You Implement Lean Warehousing?
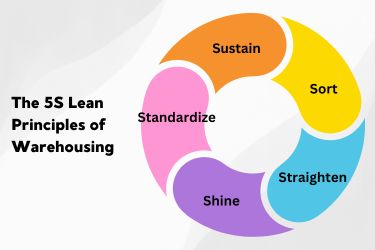
Lean warehousing is a management process similar to lean manufacturing that seeks to maximize available warehouse space and labor to reduce waste and costs. This is accomplished by implementing five principles that are applied across each area of a warehouse operation: Sort, Straighten/Set in Order, Shine, Standardize and Sustain.
To help supply chain professionals meet customer demand more efficiently and more easily go about adopting lean warehousing, below is a breakdown of these core lean warehousing principles:
Sort
The Sort process is one in which warehouse operations are analyzed to ensure only essential tools and supplies are utilized. You can think of this part of applying lean warehousing as taking an inventory of resources and spaces to identify and eliminate waste. From your equipment to the lanes used for transporting finished goods, evaluate each area of your warehouse to see if waste can be found. If it is found, eliminate it or look for alternatives that result in less waste.
This can improve efficiency by providing workers with the right tools in the right areas of a warehouse for each task. Instead of having to sort through unnecessary tools and resources along each iteration of the order fulfillment process, a lean warehouse only utilizes essential tools. As an added benefit, this part of the process can keep a warehouse clean and open up more usable space.
Straighten
Also sometimes referred to as Set in Order, Straighten is the part of lean warehousing that ensures all work areas are neat and orderly. Any experienced warehousing professional knows that cluttered work areas lead to accidents and injuries, and they also cause inefficiency.
Straightened workspaces that are organized and orderly allow employees to find what they’re looking for more quickly. Implementing steps to straighten workspaces also helps to speed along the process of adopting lean warehousing because attempting to adopt lean principles in a disorganized workspace is an exercise in futility.
Shine
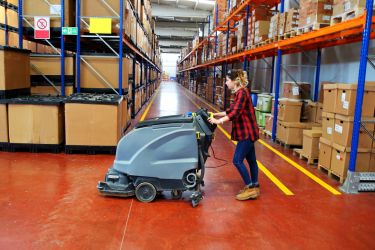
The Shine step in lean warehousing is a part of continually improving spaces. When implementing Shine, employees are encouraged to clean and secure workspaces like loading docks at the end of each shift. This keeps workspaces orderly, but it can also improve productivity.
When workers take pride in their workspaces and feel a personal connection to the look of a workspace, they tend to be more productive. When surrounded by clutter and messes, productivity usually reflects this disorganization. Additionally, cluttered workspaces contribute to employee accidents and injuries, potentially causing injured workers to require time off. This further hurts productivity and can lead to bottlenecks in supply chains.
Standardize
Adopting lean warehousing also means standardizing protocols so that they can be codified and shared. Effective lean warehouse management requires that all members of a warehouse organization utilize the same warehouse processes. If there is no standardization of processes, the concept of creating a lean warehouse falls apart.
If you’re planning on implementing lean warehousing practices at your organization, consider drafting a standard operating procedure (SOP) manual for your workers. Your SOP manual should incorporate Shine Standardize and Sustain principles along with details explaining what is expected of each employee in implementing these practices. Once completed, your SOP manual should be provided to each new hire during onboarding, and it should also be referenced in regular training sessions throughout the year.
Sustain
Lastly, the Sustain portion of lean warehousing is vital to the process as any plan is only as good as its execution. Applying lean warehousing in a sustainable manner means continually monitoring the implementation of and improving upon the principles of lean warehousing. Using principles outlined in the Standardize step of lean warehousing, employees using Sustain principles are encouraged to be mindful of their actions to support the entire process each day.
This can help to reduce operational costs, one of the biggest reasons for outsourcing in supply chain management, and meet customer demands more efficiently, thereby improving customer relations overall and customer retention in the long term. Sustained operations in lean warehousing also support team-building as everyone is involved in the initiative together. Building camaraderie in this way becomes a feedback loop of support as employees encourage one another to stay on top of lean warehousing practices.
How to Encourage Adherence to Lean Warehousing Principles
Employers can further these efforts by holding regular training and check-in sessions. Collateral can be placed around a warehouse reminding employees of the shared goals of lean warehousing, and incentives may even be offered to help improve efforts in applying lean warehousing principles.
Some employers also find success in gamifying workplace initiatives. By creating a friendly competition that rewards outstanding employees for exemplifying lean warehousing principles, you encourage positive actions. Consider holding a weekly or monthly contest in which employees nominate one another for leadership in each of the five principles of lean warehousing. The employee who wins may receive a small reward like a gift card or additional time off.
How Lean Warehousing Affects Long-Term Success
The goal of lean warehousing is to do more with less without sacrificing quality. This last bit is important as there are plenty of ways to cut corners and improve efficiency in logistics, but most methods require warehousing and inventory management professionals to give up portions of quality control. As any experienced warehouse manager knows, sacrificing quality can lead to bottlenecks in supply chains, delayed shipments, lost inventory and dissatisfied customers.
When implemented correctly according to the five principles of lean warehousing, these processes have the potential to improve efficiency in the long term. With this stated, you should not feel like you need to implement all elements of a lean warehousing plan all at once. In many cases, it may be better to improve on different areas of your operation incrementally. Attempting a sudden and radical shift in operations may cause your efforts to fail, especially if your warehouse operations have been using traditional workflows for a long time.
Monitoring and Improving Are Important As Well
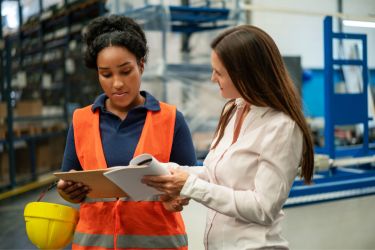
Once you’ve implemented lean warehousing principles, monitoring and improving upon your efforts play vital parts in the overall success or failure of your efforts. This has to do with the Standardize and Sustain portions of lean warehousing.
In Standardize, your goal is to achieve consistency across all parts of your warehousing operation. Having a written plan that is provided to and followed by all workers is essential for success. In Sustain, workers continue to abide by the standards set forth in Standardize. By monitoring to ensure Standardize is being followed and improving upon processes to support Sustain, your operations are more likely to see success.
Keep in mind that Standardize does not mean that your protocols are set in stone, and Sustain does not mean that you must continue to follow principles that don’t work. Lean warehousing may follow similar practices across most warehouses, but this does not mean that every operation must follow the same principles.
What works for your operation may not work for another and vice versa. Your monitoring will show you where improvements can be made, so don’t get stuck on certain ideas just because you’ve included them in your Standardize protocols or because other warehouses have implemented specific actions.
Contact Pallet Market Inc to Learn More About Improving Warehouse Operations & Efficiency
To discover how your warehouse can experience improved efficiency and save on costs, contact Pallet Market Inc. We specialize in providing solutions to enhance warehousing and logistics operations, and our team helps pallet suppliers maximize efficiency and improve customer retention.
Call Pallet Market Inc. today at (909) 356-1263, or get a quote right now.