One of the most crucial aspects of running a warehouse facility efficiently is to hire warehouse quality control talent that pays close attention to details. Implementing effective quality control (QC) can save the facility money by identifying and reducing wasted orders, time, energy, and materials. Here are essential warehouse quality control best practices.
Quality Control Resources
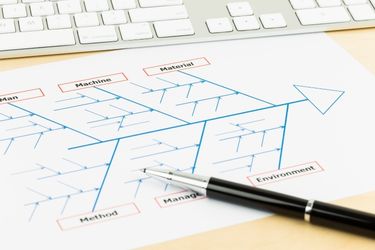
In order to meet warehouse quality control standards, your operation must be equipped with the right tools that help communicate system problems requiring solutions. Here are some of the most important tools used for quality control in the logistics industry:
- Cause-and-effect chart: Also known as a fishbone diagram, this visual tool reveals the potential causes of a warehouse issue.
- Daily checklist: QC personnel need to check off a list of priorities for inspection.
- Flowcharts: These charts are used to illustrate and simplify workflow steps.
- Histograms of warehouse data: Histograms are charts that group data in ways that make it easy to visualize comparing variables and their frequencies.
- Pareto chart: This type of histogram used by warehouse managers reflects the frequency of issues such as system errors.
- Control chart: This chart shows how a workflow evolves over time.
- Scatter diagram: You can get a better understanding of the relationship between two variables with this tool.
Investing in QC Software
Investing in warehouse management software integrated with bar code scanners allows your team to easily and quickly locate inventory items. The platform should include quality control features that let you run tests on order processing and packaging. It keeps your warehouse at the pace of other modern warehouses that have gone through digital transformation, while it makes your facility more competitive than a firm that lacks the technology.
Your software's quality control features should allow for processing quality orders that move items from the QC department to another location. Item sampling is a feature for monitoring and controlling how often an item goes to the QC team. Another useful feature for a warehouse QC team is the capability of generating quality orders automatically. It's also important that your software provides you with analytics on the metrics crucial to improving your quality control practices.
Keys to Reducing Operating Costs
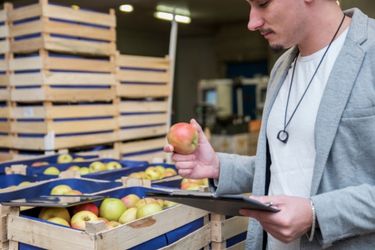
Knowing how to lower operating expenses is one of the main challenges of a warehouse manager. Customer returns can cut into profits, but they are essential to ensure customer satisfaction, which has a major impact on repeat business.
Part of your goal to streamline the warehouse should be to identify issues that trigger returns and implement solutions for reducing them. Here are common ways for a warehouse to reduce operating costs:
- Inspect for damaged items regularly: It's best to spot product defects in your inventory early so the items don't take up valuable space in the distribution area.
- Reduce mis-picks: A mis-pick is when the picker selects the wrong item that doesn't match the order. It creates a series of costly problems, such as additional shipping and placing the item back into inventory properly.
- Use modern verification methods: Orders can be verified with scanners and processes that reduce the need for time-consuming manual methods. Scan-to-Cart is a method in which an operator scans items for a batch of orders on a picking cart. Weight verification scanning is another method that reduces shipping errors.
Tips for Improving Quality Control
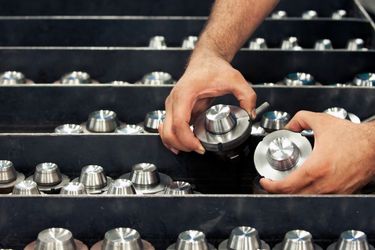
Warehouse efficiency can be achieved with the right people and technology. That means facilitating a positive workplace that acknowledges team players as valuable. A goal of any successful employer is to attract quality talent that will stay and grow with the team. The alternative, which is high turnover, can be expensive. The average salary of a warehouse QC specialist ranges from $25,000 to $44,000. Here are tips to maintain and improve your QC team:
- Focus on customer satisfaction: Make the customer the primary focus of your order processing and QC teams.
- Organize warehouse layout efficiency: Space optimization should be a top concern for every warehouse. Designate specific areas for defective products and mis-picks that are out of the way from normal activity.
- Provide staff training: A warehouse is like a jungle to some workers until they become familiar with inventory placements. Teach employees strategies that will help them to be more time-efficient with order fulfillment.
- Develop good supplier relationships: The better your QC team communicates with suppliers, the more likely they'll work together cohesively.
- Inspect individual orders closely: Frontline QC specialists should be trained to thoroughly inspect orders to confirm the information is accurate. Your QC team should be able to verify the contents and packaging. They should be responsible for flagging orders that need to be redone.
Conclusion
Practicing warehouse quality control can make your facility more profitable. Much of it comes down to effective communication among team members. One way to make your warehousing and distribution more efficient is to develop strategic plans for pallet organization, utilization, and recycling. And, where you’re ready to buy pallets near you, the pallet pros at Pallet Market are here to help.